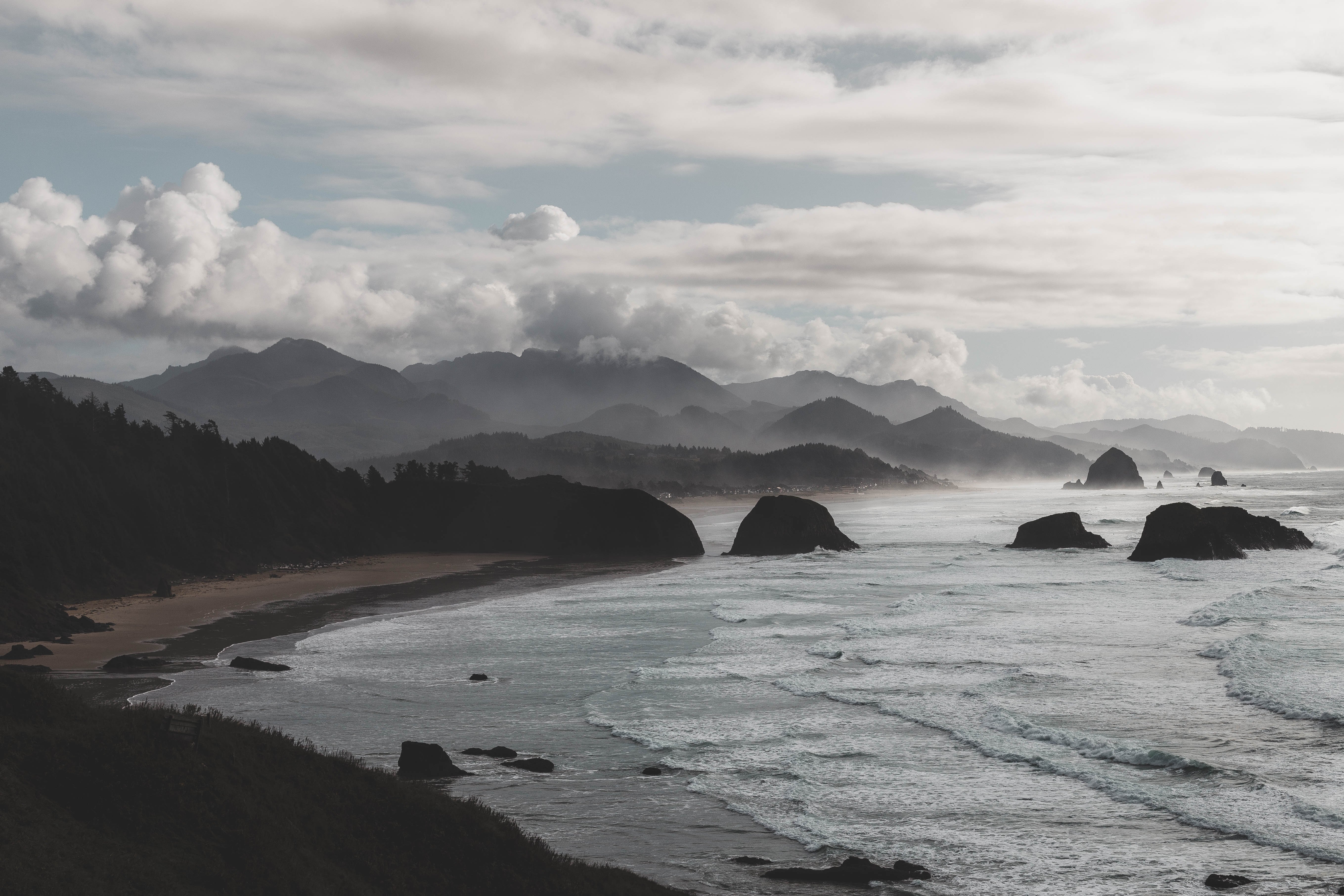
Loading grains in the Pacific Northwest can be a real test of patience. For shipowners not familiar with the Pacific Northwest, where it rains approximately 150 to 180 days per year, with rainfall totals averaging 40 inches per year, it is important to maximise loading during periods of light rain and to prevent vessel delays while avoiding moisture damage to the cargo during periods of moderate to heavy rain.
Vessel delays could lead to disputes between the charterer and the owner. In cases where the vessel is delayed by rain, the terminal will bill the charterer and the charterer will deduct the amount from the hire owed to the owner. The owner then must try to recover the money back from the charterer.
The UK P&I Club offers the following advice to shipowners and charterers who load grains at ports in Washington and Oregon.
Grain elevators in the Pacific Northwest have recently been aggressively pressing vessels to continue loading during periods of other than light rain, sometimes by threat of order to vacate the berth, other times by financial penalty (locally termed ‘Tariff for Delay of Berth’) for delays. Furthermore, masters are usually under instruction to clause the Mate’s Receipts, and subsequently the Ocean Bill of Lading, to reflect that the cargo was loaded during inclement weather and therefore its condition is unknown. This of course leads to the issue of the banks and financial institutions refusing to accept the documents for transfer of funds. (LOPs are typically submitted to agents in this instance, officially addressing loading conditions in light rainfall).
The vessels are usually detained or arrested alongside the berth until the issue has been resolved, usually by the issuance of a Letter of Protest by the vessel. Penalties are then levied by the elevator for failure to vacate the berth and loss of loading time, as well as by the charterer for off hire time. Most Mate’s Receipts have “Said to be, Said to Weigh” already printed on them, as the vessel has no knowledge as to the quality/condition of the goods.
The load order for a shipment of grain will specify what the maximum moisture content for that product is, typically around 12%. During loading, the Federal Grain Inspection Service (FGIS) or Washington State Department of Agriculture WSDA will be continuously sampling and grading the cargo, and will have a running count of the moisture content. This has sometimes been used to give the vessel a false impression as to how much moisture/rain the cargo has absorbed or was exposed to. It does not reflect the exposed surface of the cargo which the surface at the time is exposed; however, multiple layers of precipitation-exposed cargo may lay atop one another.
Surveyors are called on to attend vessels and assist the master with the loading of grain cargoes during periods of inclement weather. As a general guideline, it is suggested that if grain dust is observed exiting the cargo hold during loading in light precipitation, then continuation of loading may be considered. Once the precipitation reaches a rate sufficient to displace the emanating grain dust, the halting of loading operations can be considered by the master. Obviously, this means that some moisture may reach the cargo whilst the hatch covers are being closed. We are unaware of any claims being made when this advice has been followed.
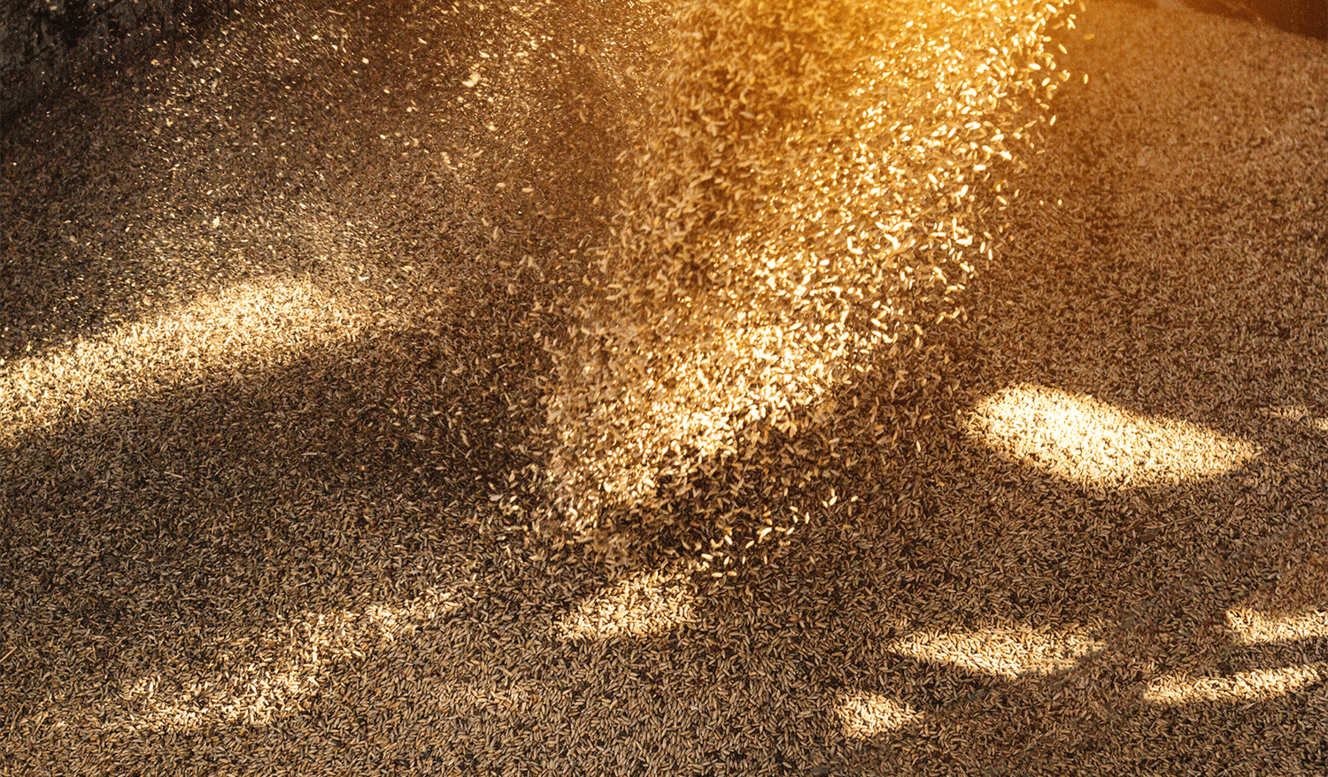
In an effort to reduce the risk of moisture damage and the aggravation caused, some terminals within the Columbia River have been using reducers with rubber gaskets that fit over the cement ports in a vessel’s hatch covers. The reducer attaches to the bottom of the load spout and usually has air-inflated rubber inner tubes fixed around the outside of the reducer. The ship then opens the cement port and the reducer is placed into the cement port opening. The load spout is lowered until the inner tube is compressed, making a seal on the hatch cover. The ship will then open the hold vents to reduce any pressure created in the hold when the cargo is loaded.
The amount of moisture entering the hold through any small leak in the seal is typically less than would enter the hold when the hatch covers are open and are then closed at the onset of rain. Surveyors have had experience of the use of this type of reducer whilst loading soda ash at Terminal No. 4, Port of Portland, Portland, Oregon, and have not had any adverse feedback from receivers. Soda ash, as you will appreciate, is extremely sensitive to moisture ingress and sets up hard clumps, almost like cement. The one issue with loading through the cement ports is that when the cover is replaced, it is imperative that the gasket is in good condition and that the securing bolts are tightened in the correct order, i.e. diametrically opposite. Of course, when using the reducers, it is only possible to fill the hold to approximately 70% of capacity before the cone of cargo reaches the underside of the hatch cover. In order to ‘top off’ or level the cargo, the hatch covers must be opened. Further to closed hatch loading, after completion of loading, each hatch cover must be opened, and hatch cover gaskets, hatch cover coaming channels, compression bars and drains must be cleaned to allow proper drainage of seawater should the vessel experience water on deck during the voyage.
We would like to extend great thanks to Dave Shoemaker of Duncan Shoemaker & Associates, for his contribution with this article (https://www.duncanshoemaker.com/).